
Maximum step-pulse frequency is 100KHz,which is suitable for the servo or stepping motor 3. Support for 4-axis linkage, you can connect four stepper motor drives or servo drives 2. 5 Mechanical dimensions diagram: Prepare: Installation the Mach3: Software license application: Installation the software of the USB motion card: Connecting the USB cable to the PC and the motion card: Installing the motion card plug-in config for mach3: Mach3 X Y Z A Axis config as shown below: Config => Ports and Pins): Motor tuning setup as shown below: (Config => Motor Tuning) The Mach3 Menu => Config => Homing/Limits dialog: Setup the input signal: Setup the Output signals: Spindle speed control (0-10V) Setup: Mach3 MPG Setup. 4 Basic connection diagram (an Overview). Please strictly follow the instructions and warnings using this product.any direct / indirect personal injury, our company does not assume any responsibility.ģ Contents Mach3 USB Motion Card (STB4100) Installation Manual. Recommends that users install the emergency stop button and make sure the button is functioning properly.
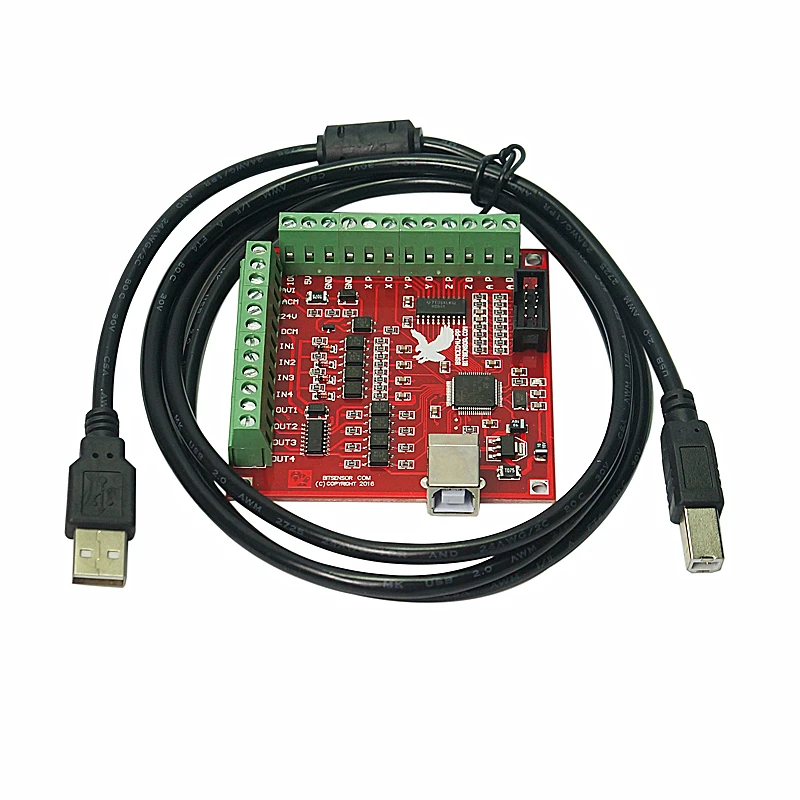
Employment Opportunity / RFQ (Request for Quote).2 The motion control card for machine control, with strong professional.requires the operator to have the relevant expertise!if used improperly, may appear an accident, please strictly follow the instructions and warnings using this product if you are not sure, consulting engineers for help.first time users, if you are not familiar with the product and software features Mach3 In your test product, make sure the machine's power switch on hand, you can quickly turn off the power.
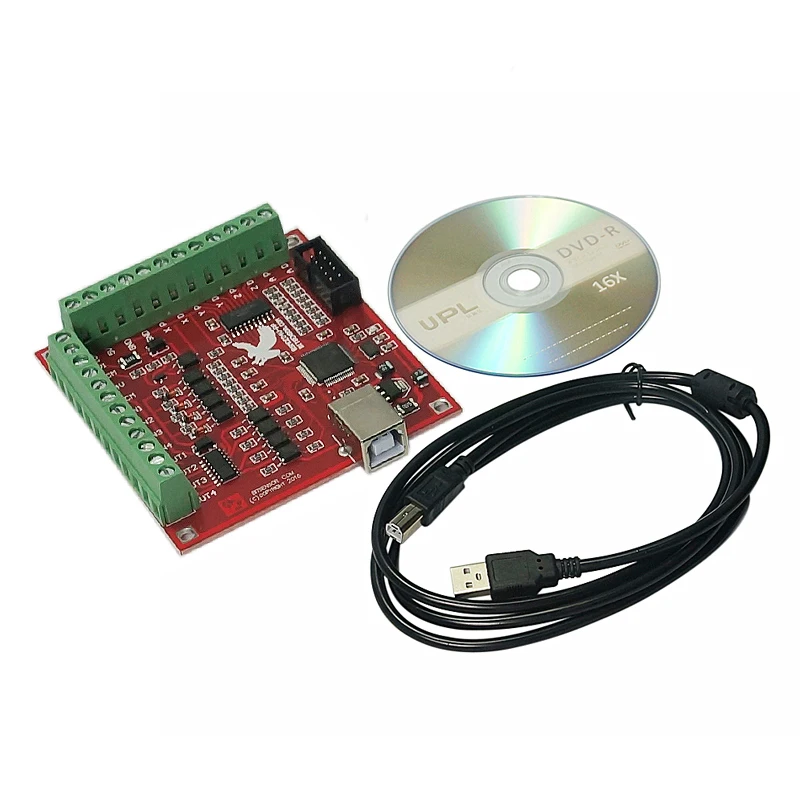
Quick Navigation SmoothStepper Motion Control Top I can live with my current design choices at this point. Once you know the limits of each device, you can then assess the limits of performance and know where the "bottlenecks" are. I also realize that my lead screw may well whip at the higher rates and I did get slight whipping around 1200 RPM using an electric drill for testing. The ESS can fully drive the G540 to its 300KHZ max. Hence the choice of ESS which can do 4MHZ step pulse rates.
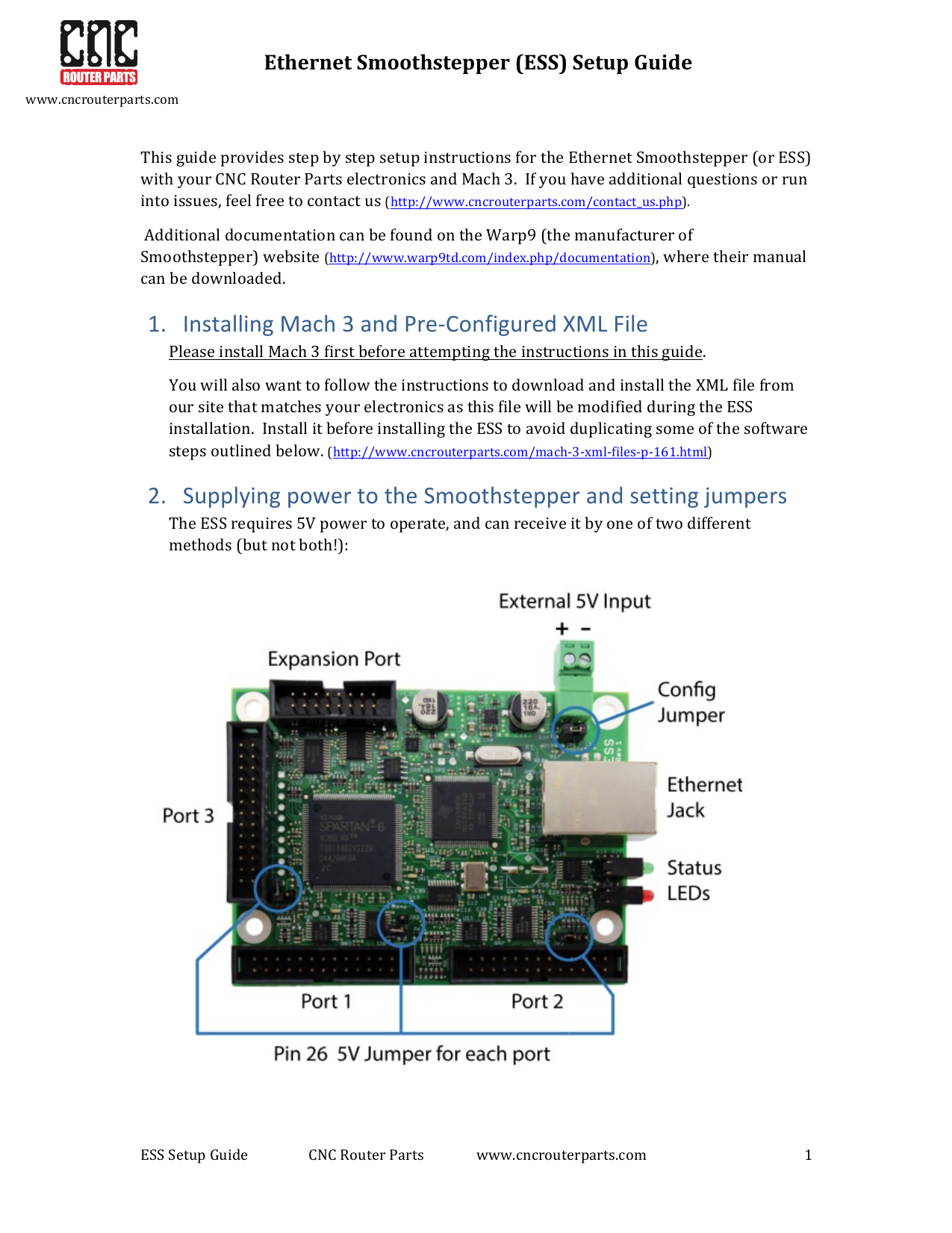
To allow the potential of higher RPM, I decided for a device that could go much faster without pushing Mach_3 to the edge. At this RPM and 10 micro-steps requires a step frequency of 36.7KHZ. What I didn't realize at the time was that in order to get 100 IPM jog rate the direct drive motor must run at 1100RPM. My reason for choosing the ESS was that I had bought a Gecko G540 4-axis controller which has 10 micro-stepping feature. My diy cnc is more of a proof-of-concept since I don't know yet what I want to make with it.
